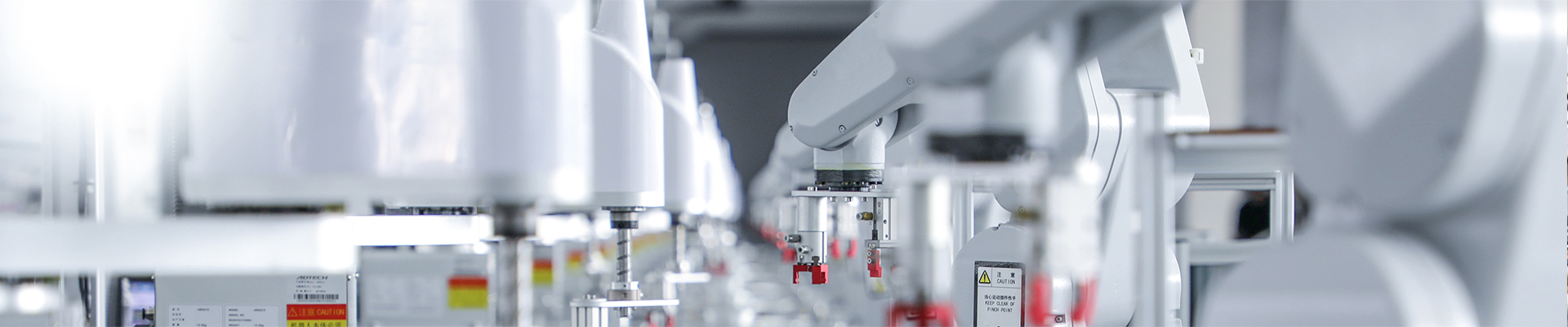
A Comprehensive Guide to the Fully Automatic Valve Coil Production Line
2025-05-19 10:25When I learned about the Fully Automatic Valve Coil Production Line, I saw it was more than a factory machine. It changes industries like cars, communication, and hydraulic systems. This system works fast and does hard tasks with great accuracy. It easily handles more work as demand grows, helping companies stay competitive. Its smart Automatic Valve Coil winding machine makes production smooth and efficient, giving reliable results every time.
Key Takeaways
The Automatic Valve Coil Line makes coils faster and more accurate.
It can make up to 2,000 coils every hour, perfect for busy industries.
Automation cuts labor costs by removing boring, repeated tasks, saving money.
Live monitoring finds problems fast, reducing delays and keeping work smooth.
The line is flexible and can adjust to different coil shapes and sizes.
Careful checks ensure only perfect coils are sent, making customers satisfied.
Its energy-saving design uses less power, helping the planet and saving money.
Buying this system pays off quickly and helps businesses grow faster.
What is a Fully Automatic Valve Coil Production Line?
Definition and Overview
When I first learned about the Fully Automatic Valve Coil Production Line, I saw it was more than a simple machine. It’s a system that automates making valve coils, which are important in many industries. This line uses advanced tools and precise engineering to give steady results. It includes machines like the Automatic Valve Coil Winding Machine, which winds coils quickly and accurately.
The system works smoothly, doing jobs like feeding wire, winding, soldering, and testing without needing people to help. Its smart design lets factories make thousands of coils every hour, easily meeting high demands. I think it’s a big improvement for companies wanting to work faster and keep quality high.
Importance in Modern Manufacturing
Today, factories need automation to stay competitive. The Fully Automatic Valve Coil Production Line is key to this change. It removes the need for people to do repetitive tasks, cutting mistakes and boosting output. I’ve seen how it can make production much faster while staying precise.
Factories depend on systems like this to meet the need for top-quality products. For example, the Automatic Valve Coil Winding Machine makes sure every coil is made perfectly. This accuracy is very important in industries where small mistakes can cause big problems. By using this technology, companies can get reliable results and stay ahead of others.
Key Applications Across Industries
The Fully Automatic Valve Coil Production Line is very useful in many industries. It helps make coils for cars, like those used in relays and solenoids, so vehicles run well. Communication systems use it to make coils for signals, improving performance and reliability.
Hydraulic systems also need valve coils for accurate control. This line ensures these coils are made to high standards, making systems work better. I’ve seen factories adjust the Automatic Valve Coil Winding Machine to make coils for special uses, showing how flexible it is for different needs.
Tip: If you work in these industries, getting this production line can improve your business. It’s not just a machine; it’s a way to make better products and earn more money.
Components of the Production Line
Automatic Valve Coil Winding Machine
The Automatic Valve Coil Winding Machine is the main part. It winds coils very fast and with great accuracy. This ensures every coil meets top standards. With 12 spindles, it can make many coils at once. This makes it ideal for factories needing to produce a lot.
What’s amazing is how much it can do. It doesn’t just wind coils; it also solders, tests, and removes defective ones. The touchscreen and PLC controls are simple to use, even for beginners. Its AI system finds defects, so every coil is perfect.
Here’s a quick summary of its features:
This machine is the key to the production line. It ensures every coil is made with the same high quality.
Wire Feeding and Tensioning System
The wire feeding and tensioning system is very important. It makes sure the wire moves smoothly during winding. This prevents tangles or breaks that could slow things down.
Its precision is what makes it special. It keeps the wire at the right tension, which is needed for strong, even coils. Without this, coils might not be as good. This system ensures every coil is perfect.
It’s also easy to maintain and lasts a long time. This means less time fixing it and more time making coils. For factories, this reliability is a big advantage.
Insulation and Coating Unit
The insulation and coating unit makes the coils strong and durable. It adds a protective layer to each coil. This helps them survive heat, moisture, and stress.
This unit uses advanced materials like polyester and Kapton for taping. These materials protect the coils while staying flexible. It also applies the coating evenly, making the coils more reliable.
What stands out is how fast it works without losing quality. This makes it a must-have for industries like cars and communication. These industries need products they can trust.
Note: Choosing a production line with these parts ensures great results. It’s a smart move for any factory wanting to stay competitive.
Quality Inspection and Testing Station
Quality is the heart of making good products. The Quality Inspection and Testing Station makes sure every coil is top-notch. It uses smart tools to find problems and check reliability.
Here’s why this station is special:
Automated Testing: It quickly checks resistance, insulation, and other key features. This system works fast and avoids mistakes.
Defect Detection: Coils that fail the test are removed automatically. Only perfect coils move forward.
Real-Time Monitoring: The station shows live updates during testing. This helps workers fix problems right away.
This station is very important for industries like cars and communication. These industries need products they can trust. The testing station ensures every coil works well, even in tough conditions.
Tip: Buying a production line with a strong testing station saves money. It stops bad products from reaching customers and improves your brand’s image.
Packaging and Final Assembly Unit
The last step is just as important as the first. The Packaging and Final Assembly Unit gets the coils ready to ship. It combines speed and accuracy to finish production smoothly.
Here’s what it does:
Automatic Assembly: It puts the coils together perfectly, adding pins and parts.
Protective Packaging: Coils are packed safely to avoid damage during shipping. The process is fully automated, saving time.
Labeling and Sorting: Packages are labeled with batch numbers and details. They are also sorted for easy delivery.
This unit makes production faster while keeping quality high. It ensures coils reach customers safely and ready to use.
Note: A good packaging unit doesn’t just protect the product. It also makes customers happy by delivering reliable and professional-looking coils.
These two parts—the testing station and packaging unit—finish the Fully Automatic Valve Coil Production Line. Together, they make sure every coil is high-quality and ready for customers.
How the Production Line Works
Step-by-Step Workflow
Wire Feeding and Preparation
The first step is feeding and preparing the wire. The system pulls wire from spools automatically. It keeps the wire smooth and untangled. The tension is adjusted carefully to keep the wire strong.
This step stops problems later in the process. By keeping the tension right, the system makes sure coils are even and dependable. This preparation is very important for making good products.
Coil Winding Process
The coil winding step is where the main work happens. The Automatic Valve Coil Winding Machine winds the wire into perfect coils. It works super fast, reaching speeds of 18,000 RPM. Its CNC control ensures every coil is the same and high-quality.
This machine is very efficient. It can wind many coils at once, saving time and increasing production. This step is the most important part, getting the coils ready for the next stages.
Insulation and Coating Application
After winding, the coils get insulation and coating. This step adds a protective layer to make them strong and safe from heat or moisture. Materials like polyester and Kapton are used for flexibility and strength.
The coating is applied evenly, which makes the coils more reliable. This is especially important for industries like cars and communication. The process is quick and accurate, keeping production on track.
Quality Testing and Inspection
Testing is the most important step. The inspection station checks each coil for problems. Automated tools measure resistance, insulation, and other features.
This station is great because it removes bad coils automatically. It saves time and ensures only good coils move forward. Real-time updates help workers fix issues quickly, keeping everything running smoothly.
Final Assembly and Packaging
The last step is putting the coils together and packing them. The system adds pins and other parts to the coils. Then, it packs them safely to avoid damage during shipping.
The unit also labels and sorts the packages for easy delivery. It works fast and accurately, making sure the coils reach customers in perfect shape. This step finishes the production process.
Integration of Automation and Robotics
Automation and robotics make the production line super efficient. These technologies improve how the system works:
Robots replace people for precise and error-free tasks.
Automated lines with AGVs make production faster and cheaper.
Inspection and assembly automation ensure accurate and reliable products.
Robotic glue systems improve precision in healthcare uses.
Vision-guided robots make production faster and more flexible.
These upgrades make the Fully Automatic Valve Coil Production Line amazing. Automation helps factories produce faster, better, and at lower costs.
Tip: Using automation and robotics isn’t just about speed. It helps businesses stay ahead in a competitive market.
Technical Specifications
Key Specifications Overview
The Fully Automatic Valve Coil Production Line is built for speed and accuracy. It works fast, reaching up to 18,000 RPM, while staying precise. This makes it a great tool for factories.
Another great feature is its flexibility. It can handle different coil designs, wire types, and valve sizes. This means factories can make many products without losing quality. Its energy-saving design also helps cut costs, making it a smart choice for businesses.
Table of Specifications
Automatic Valve Coil Winding Machine Specifications
The Automatic Valve Coil Winding Machine is the most important part. It is designed to make high-quality coils every time. Here’s a simple breakdown:
This machine works fast and ensures every coil is made perfectly.
Production Line Capacity and Speed
The production line can make up to 2,000 coils every hour. This is great for factories that need to produce a lot. Its multi-spindle design lets it wind many coils at once, saving time.
I’ve seen how this system helps factories meet deadlines. It keeps quality high while working quickly. Real-time monitoring also helps avoid delays and keeps everything running smoothly.
Power and Energy Requirements
Saving energy is very important for factories. The Fully Automatic Valve Coil Production Line uses power wisely while still working well. Here’s a quick look at its energy details:
This design saves energy and supports eco-friendly manufacturing. It’s a great choice for businesses that care about the environment.
Tip: Choosing an energy-efficient production line saves money and helps the planet.
Features of the Fully Automatic Valve Coil Production Line
High Precision and Consistency
Precision is very important in manufacturing. This production line makes coils with perfect accuracy. Every coil matches exact specifications, which is crucial for industries like cars and communication. Even small mistakes can cause big problems.
The system uses smart controls to adjust settings instantly. This ensures coils are wound correctly every time. It removes errors, even when working at high speeds. This precision improves product quality and builds customer trust.
The production line can handle many coil designs without losing accuracy. Simple relay coils or complex solenoids are made perfectly. This flexibility helps factories meet different market needs.
Advanced Automatic Valve Coil Winding Machine Technology
The winding machine is the main part of this system. Its advanced features make it better than older machines. It works super fast, reaching speeds of 18,000 RPM. It winds many coils at once with great precision.
The CNC system makes sure every coil is exactly the same. This keeps quality high. The soldering process uses electric welding, creating strong and reliable connections.
The machine is easy to use with its touchscreen controls. Workers can quickly set it up for different coil designs. Switching between designs is fast and saves time. This adaptability helps factories stay competitive in busy markets.
Real-Time Monitoring and Control
Real-time monitoring makes this production line very efficient. It collects data from sensors and machines, showing how production is going. Problems are spotted early, saving time and resources.
Here’s what monitoring does:
Tracks production to keep everything running smoothly.
Finds defects quickly so they can be fixed right away.
Shows machine usage to improve efficiency and reduce waste.
These features help factories work better and make more money. Monitoring reduces downtime and keeps production moving.
Being able to watch and control the process in real-time is a big advantage. It improves efficiency and ensures every coil is high-quality. For factories, this is the best way to make great products while producing more.
Customization Options for Different Coil Types
When I first saw the Fully Automatic Valve Coil Production Line, I was impressed. It can adjust to many coil designs. This makes it very useful for manufacturers. Whether you need simple relay coils or complex solenoids, this system can do it all.
Made to Fit Your Needs
The production line has many ways to customize coils. Here are some of its best features:
Wire Material Compatibility: It works with copper, aluminum, and enameled wires. You can pick the best wire for your needs.
Adjustable Winding Methods: It allows single-layer, multi-layer, or bifilar winding. This helps make coils for different industries.
Variable Coil Sizes: It handles small micro-coils and large industrial coils.
Tip: If your business serves many industries, this flexibility is great. You can make more products without buying extra machines.
Smart Programming Features
The CNC-controlled winding machine is very advanced. It lets you control every part of the coil-making process. For example:
These options help make coils that meet exact needs. I’ve seen how this control improves quality and reduces waste.
Applications for Different Industries
Each industry has special needs, and this system delivers. For car makers, it creates strong solenoids. In communication, it makes coils for better signals. Hydraulic systems get durable, precise valve coils.
Note: Customization isn’t just about meeting specs. It’s about making products that impress customers.
Why Customization is Important
I think customization helps businesses stay ahead. It lets you meet market demands and offer unique solutions. With this production line, you’re not just making coils—you’re growing your business.
Benefits for Manufacturers
Increased Production Efficiency
The Fully Automatic Valve Coil Production Line makes work faster. It automates tasks like wire feeding and coil winding. This speeds up production and saves time. It can wind 20 coils at once at 18,000 RPM. This boosts productivity to a whole new level.
This system also reduces delays. It has real-time monitoring to keep everything running smoothly. If something goes wrong, it spots the issue right away. This prevents downtime and keeps production on schedule.
The Automatic Valve Coil Winding Machine is very important here. It works fast and accurately, making thousands of coils per hour. This helps businesses grow and meet higher demands.
Tip: Using this system means faster work and happier customers.
Cost Savings Through Automation
Automation isn’t just quick—it saves money too. This system cuts costs by improving how things are done. It uses smart tools to predict problems and avoid breakdowns. This reduces expensive repairs and wasted time.
Here’s how it saves money:
It lowers costs by automating tasks.
Sensors find problems early, stopping costly damage.
Fewer mistakes happen, so there’s less waste.
These savings can be used to grow the business or improve services.
Note: Automation is a smart way to save money and grow.
Enhanced Product Quality and Reliability
Making high-quality products is very important. This system ensures every coil is perfect. The inspection station checks each coil and removes bad ones. Only the best products go to customers.
The Automatic Valve Coil Winding Machine makes sure every coil is made with precision. Its CNC system keeps everything consistent, even at high speeds. This is very important for industries like cars and communication, where small mistakes can cause big issues.
Reliable products make customers happy. When customers trust your products, they keep buying from you. This increases sales and builds a strong reputation.
Tip: Great products bring loyal customers and long-term success.
Scalability for Large-Scale Manufacturing
Growing a business needs systems that can handle more work. The Fully Automatic Valve Coil Production Line makes this easy. It produces up to 2,000 coils every hour without slowing down or losing quality. This is great for factories with big orders to fill.
Its multi-spindle design is very efficient. It winds many coils at once, saving time and increasing production. Another benefit is its flexibility. It works with different coil sizes and designs, making it useful for many industries. Whether for cars or communication, this system fits your needs.
Real-time monitoring is a huge help. It watches every step of production to ensure smooth operations. If there’s a problem, workers are alerted right away. This reduces delays and helps meet deadlines.
Tip: A scalable system like this helps businesses grow without delays.
Reduced Downtime and Maintenance Costs
When machines stop, businesses lose money. The Fully Automatic Valve Coil Production Line helps avoid this. Its smart sensors find problems early, stopping big breakdowns.
The machine is built for easy maintenance. Parts are simple to reach, so repairs are quick. Strong materials make it last longer, reducing wear and tear. This means fewer stops and lower repair costs.
Automation also helps a lot. The system predicts issues before they happen, keeping production smooth. Factories can focus on making products instead of fixing machines.
Note: Picking a low-maintenance system saves money and keeps work on track.
Real-World Use Cases and Testimonials
Case Study: Automotive Industry
I visited a car factory and saw how the Fully Automatic Valve Coil Production Line changed their work. They used it to make solenoid coils for fuel injectors and transmissions. These parts needed to be very precise for cars to work well.
The system could wind 20 coils at once at 18,000 RPM. This helped the factory finish work quickly without losing quality. The automated inspection station checked every coil and removed bad ones right away. This saved both time and materials.
An engineer told me the system cut their costs by 30%. They didn’t need workers for repetitive jobs anymore. Instead, their team focused on creating new ideas. The factory also made 25% more products, which helped them get more deals with top car companies.
Insight: If you’re in the car business, this system helps you make better parts faster and cheaper.
Case Study: Communication Systems
I also saw this system in a communication factory. They used it to make coils for antennas and signal amplifiers. These coils had to be very reliable for smooth communication.
The manager said the system’s customization made it easy to create different coil sizes and designs. They could switch between tasks quickly to meet customer needs. The real-time monitoring kept quality high, even at fast speeds.
The results were amazing. The factory cut production time by 40% and improved product reliability. This gave them an edge over competitors. Their customers loved the strong and dependable coils, leading to long-term deals.
Tip: In communication, reliability is key. This system ensures your products are top-notch.
Testimonials from Manufacturers
Manufacturers using the Fully Automatic Valve Coil Production Line shared great feedback. A hydraulic systems maker said, “We now make 2,000 coils per hour with no defects.”
An automotive supplier said, “This system’s speed and precision helped us meet the demand for electric car parts. It’s a game-changer.”
A communication equipment maker added, “The system’s flexibility is incredible. We can make custom coils without delays. Our clients love the results.”
Takeaway: These stories show this system works. It’s not just a machine—it’s a way to grow and succeed.
ROI Analysis for Adopting the Technology
When deciding on new technology, I ask, "Is it worth it?" The Fully Automatic Valve Coil Production Line gives a clear and strong return on investment (ROI). Let me explain how.
1. Cost Savings Through Automation
This system removes the need for workers in repetitive tasks. By automating wire feeding, winding, and testing, factories save a lot on labor costs. One company I know reduced their coil production team by 40%. That’s a big cut in salaries and training costs.
The system also reduces material waste. Its accuracy ensures every coil is made perfectly, so there are fewer defective products. Less waste means more money saved.
Tip: Automation is an investment that saves money by cutting extra costs.
2. Boosted Productivity and Output
This system can wind 20 coils at once at 18,000 RPM. Factories can make up to 2,000 coils every hour. This speed helps businesses handle big orders fast without losing quality.
I’ve seen companies double their production using this system while keeping the same costs. More products mean more income, which helps the business grow.
3. Enhanced Product Quality and Customer Satisfaction
Good products make customers happy. The automated inspection station ensures only perfect coils are sent out. This lowers returns and complaints, saving money on fixes.
Happy customers often buy again. They also tell others about your products, which increases sales without extra marketing.
4. Long-Term Benefits and Scalability
This system isn’t just for now—it’s built for the future. It can adjust to new needs, like making different coil designs or handling bigger orders.
Its energy-saving design also cuts utility bills, adding to long-term savings. Over time, these benefits add up, making the initial cost seem small compared to the gains.
Insight: Investing in flexible technology helps your business grow and adapt to changes.
5. Quick Payback Period
Most companies I’ve talked to recover their costs in under two years. With savings, higher output, and happy customers, the system quickly pays for itself. After that, it’s all profit.
Takeaway: The Fully Automatic Valve Coil Production Line isn’t just a machine—it’s a smart way to grow your business and increase profits.
Looking at the numbers, the ROI for this system is clear. It saves money, boosts income, and prepares your business for the future. If you want to stay ahead, this is the investment to make.
The Fully Automatic Valve Coil Production Line is a big help for factories. It makes work faster, saves money, and ensures perfect results. Factories can make more products without losing quality, staying ahead of competitors.
Using smart automation is not just a good idea—it’s necessary. It keeps factories ready for today’s fast-changing market. With SIPU’s help, businesses can easily start using this advanced system.
Take Action: Don’t delay improving your factory. Check out SIPU’s Fully Automatic Valve Coil Production Line now and see how it can boost your production.
FAQ
1. What industries benefit the most from this production line?
Industries like cars, communication, and hydraulics benefit greatly. It helps make solenoids, relays, and signal coils faster. Its accuracy ensures high-quality products for these important sectors.
2. How does automation reduce costs?
Automation removes repetitive tasks done by people. This lowers labor costs and prevents mistakes. It also reduces wasted materials, saving money while keeping quality high.
3. Can the system handle custom coil designs?
Yes, it can! The CNC-controlled machine allows full adjustments. You can change wire type, coil size, and winding styles. Factories can easily switch designs to meet customer needs.
4. Is it difficult to operate the production line?
No, it’s easy to use. The touchscreen and PLC controls are simple. Even new workers can learn quickly. This user-friendly system saves training time and boosts efficiency.
5. How does the system ensure product quality?
The testing station checks every coil for problems. It measures resistance, insulation, and stability. Only perfect coils move forward, ensuring customers get reliable products.
6. What is the production capacity of the system?
The system makes up to 2,000 coils per hour. Its multi-spindle design handles big orders easily. Factories can meet deadlines without losing quality.
7. Is the system energy-efficient?
Yes, it uses energy wisely. Its smart design lowers power costs. This eco-friendly feature helps both factories and the planet.
8. Why should I choose SIPU’s production line?
SIPU offers advanced technology with great precision and reliability. Their system improves manufacturing and delivers consistent results. It’s a smart choice for growing businesses.
Tip: Upgrade your factory today. SIPU’s Fully Automatic Valve Coil Production Line keeps you ahead in a competitive market.