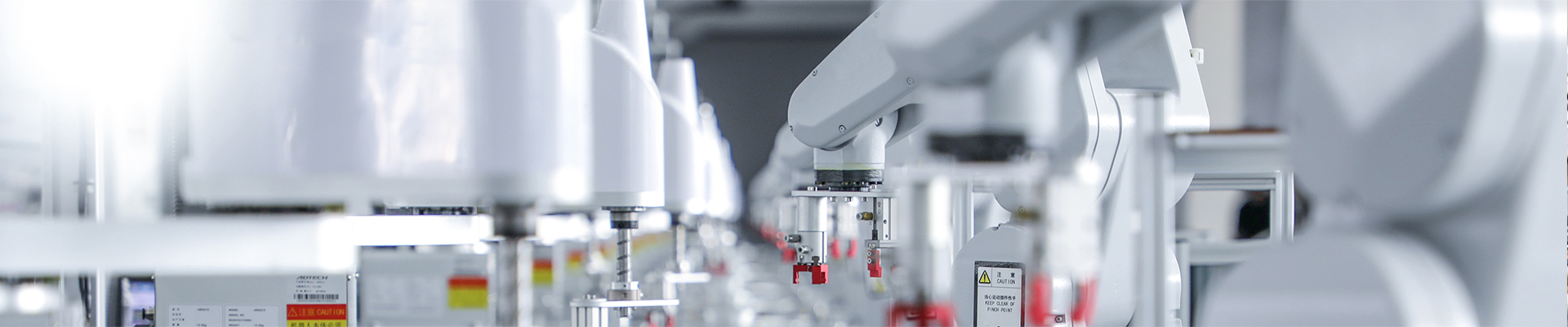
A Comprehensive Guide to Coil Production Line for Relays
2025-06-08 13:31A coil production line is important for making parts for electrical relays. It is a special setup made to create high-quality coils with accuracy and consistency. These coils are the main part of relays, helping them switch by creating electromagnetic fields. High-quality coil production is critical to ensuring the precision and reliability of relays in high-stakes applications.
SIPU's Fully Automatic Valve Coil Production Line is a new solution for modern factories. This advanced system improves every step, from winding to testing, with great speed and precision. Its smart design meets the rising need for better coil production lines in many industries.
Key Takeaways
Coil production lines make coils for relays work well and last long.
New machines, like SIPU's Automatic Coil Line, make coils faster and cheaper.
Automation helps avoid mistakes, making relay parts better and more reliable.
Good materials, like pure copper wire and strong insulation, are key for relay coil performance.
Testing and checking coils often ensure they meet rules and work correctly.
Better production lines save money by using less energy and cutting waste.
Flexible systems help factories make more relays without losing quality.
Advanced coil-making tools keep businesses ahead in industries like cars and phones.
Overview of Coil Production Line
Purpose of a Coil Production Line
A coil production line is built to make coils quickly and accurately. These coils are key parts of many relays, like the latching relay. The main goal is to simplify coil-making while keeping it precise and reliable. By using machines for tasks like pin inserting, winding, soldering , and testing, it cuts down on manual work and boosts efficiency.
Newer systems, like SIPU's Fully Automatic Valve Coil Production Line, are much better than older ones. They work faster, waste less material, and keep quality steady. For instance, modern machines can make 2000 pieces per hour, compared to just 1500 with older setups. This makes them very useful for industries like cars and telecommunications that depend on relays.
Key Processes in Coil Production
Making coils involves several steps to ensure they work well in relays. These steps include:
1.Pin Inserting: This is the foundational step where precision pins are accurately placed into the coil bobbin. Automated insertion machines are commonly used, which can handle high - volume production with consistent accuracy.
2.Coil Winding : This step wraps copper wire around a core using methods like needle-winding or linear winding. Needle-winding works for slotted cores, while linear winding spreads the wire evenly.
3.Soldering: Soldering is the process of making electrical connections firmly connected. Pins and wire ends need to be carefully soldered using high-quality solder and precise soldering techniques. We use automatic soldering machines to achieve high-quality results that save time and effort.
4.Testing and Quality Control: Special tools check the coil’s resistance, insulation, and performance. This ensures every coil meets the needed standards.
5.Conveyor Unload: Once the coils have passed all quality checks, they are unloaded from the production line via a conveyor system. They are then automatically transported to the loading station and placed in pallets.
Modern production lines improve these steps to make top-quality coils for all kinds of relays, including latching relays.
Importance in Electrical Relay Manufacturing
Coils are very important for how relays work. In electromechanical relays, the coil makes a magnetic field that moves parts inside. This movement opens or closes circuits, letting the relay control electricity. A good coil helps the relay work faster and more reliably.
For latching relays, the coil design matters even more. These relays use magnets to stay in place without needing constant power, saving energy. The coil also helps handle high-voltage spikes. A well-made coil ensures the relay works well, even in tough situations.
Modern systems, like SIPU's Fully Automatic Valve Coil Production Line, make sure every coil is top-notch. This keeps relays dependable for important uses in many industries.
SIPU's Fully Automatic Valve Coil Production Line
SIPU's Fully Automatic Valve Coil Production Line uses advanced technology to improve coil production. It automates every step, from winding to testing, for better accuracy and reliability. With CNC motors and touchscreens, it's easy to use and increases productivity.
This system helps industries like cars and telecommunications by making high-quality coils for relays, including latching relays. Its smart features reduce waste and labor costs, making it a budget-friendly choice for big factories. SIPU's design keeps your relay production competitive in today's fast-moving market.
Step-by-Step Coil Production Process
Preparing Raw Materials
The first step is getting the right materials. High-quality copper wire and insulation are needed for reliable coils. Using local suppliers is important for safety and accuracy. American suppliers follow strict rules, which lowers mistakes and delays.
To track materials, manufacturers use heat numbers. These are special codes that show where the metal came from. Mill Test Reports also give details for quality checks. Choose suppliers with strong quality programs. This ensures the coils work well in latching relays and control systems.
Tip: Check the copper wire's size and surface before using it. These affect how well the coil works in relays.
Pin Inserting
Our fully automatic coil production line has a highly integrated process flow, in which the pin insertion process is the primary link. Its professionalism and precision are directly related to the production efficiency of the entire line and the reliability of the product. Pin insertion refers to the vertical pressing of high-precision plated metal pins into the preset holes of the bobbin with a tolerance of 0.01mm.
This process builds the core channel for electromagnetic field conduction, so that the number of turns of copper wire wound later can be accurately controlled to ensure that the inductance of the coil is stable and meets the standard. At the same time, the pin is also a welding carrier. Its verticality error of less than 1° can ensure that the solder joints are full and uniform during automatic soldering, reducing the loop impedance.
Winding the Coil
Winding is a key step in making coils. Copper wire is wrapped around a core to make electromagnetic coils. Accuracy is very important here. Machines must control speed and tension to avoid wire problems. A good tension system keeps the wire steady and prevents breaks.
Modern machines let you set different options for each coil type. This is helpful for latching relays, where even layers are needed. Speed control makes sure every layer is the same, helping the coil work well in relays.
Machines control tension to keep the wire strong.
Speed control ensures even layers for better coils.
Programmable settings help make different coil designs.
Quality checks ensure the final coil meets standards.
Note: Advanced winding machines reduce mistakes and make production faster.
Soldering
Soldering involves joining pins and wire ends together to create a secure electrical connection. This critical step requires precise techniques using high-quality solder with the right melting point and conductivity. Our automated soldering machines ensure consistent soldering results, precisely controlling temperature, solder flow, and application time to create a secure, reliable joint. Apply rosin flux before soldering.
Proper soldering ensures the integrity of the circuit, allowing the coil to work effectively in relay systems, which is critical for consistent performance in high-risk applications such as automotive, telecommunications, and industrial automation.
Final Testing and Packaging
The final stage of coil production – testing and packaging – is critical to ensure that only top-quality coils make it to market. These steps are the last line of defense, carefully verifying the integrity of the coil before it is sent to the relay.
During the testing phase, the core electrical and physical properties of the coil are rigorously checked. For coils used in latching relays, specialized tests are also performed to evaluate their ability to generate and maintain a stable magnetic field. This comprehensive evaluation includes measuring the coil's resistance to ensure optimal conductivity, checking the insulation to prevent leakage, and rigorously testing its overall functionality under a variety of simulated conditions. Using advanced automated testing equipment, these evaluations are performed with amazing speed and precision, leaving no room for unqualified coils.
After successfully passing the rigorous testing test, the coils are orderly loaded into the tray. The robotic arm precisely grabs the coils and neatly arranges them in a special tray with millimeter-level accuracy, ensuring that each coil is evenly spaced and oriented. The standardized loading process not only facilitates subsequent efficient handling and circulation, but also maximizes the utilization of storage space, laying the foundation for rapid product delivery.
Studies show why these steps matter. For example:
These examples show how good testing and packaging reduce problems and improve reliability. By focusing on these steps, you ensure your relays meet top standards.
Note: Always check and adjust your testing machines regularly. This helps catch problems early and keeps the final product reliable.
Quality Control and Testing in Coil Production
Importance of Quality Control
Quality control is key to making reliable and efficient coils. Small problems, like uneven copper wire or weak insulation, can cause big issues in relays. To avoid this, strict checks are needed to meet industry rules like ASTM A653 and customer needs. These checks lower defects and ensure high standards are met.
In coil production, quality control stops bad parts from being used. This is very important for industries like cars and planes, where safety is critical. Regularly updating your quality checks helps keep standards high. For example, using tools like vendor scorecards and live tracking ensures materials meet strict rules. Catching problems early saves time, money, and keeps your reputation strong for making great relays.
Common Testing Methods
Testing ensures coils work properly in relays. Different tests check specific parts of the coil's performance to find and fix problems.
Electrical Resistance Testing
This test checks how well the coil carries electricity. It makes sure the copper wire conducts electricity as needed. If resistance is too high, the relay may not work well. Advanced tools quickly check the coil's electrical properties to match voltage and current needs.
Insulation Testing
Insulation testing checks if the coil stops electricity from leaking. Materials like Nomex and Kapton are tested to handle high voltages safely. This is very important for latching relays used in tough conditions. Good insulation keeps the coil safe and working well.
Performance Testing
Performance testing checks how the coil works in the relay. It tests if the coil makes a magnetic field and handles voltage spikes. For latching relays, it ensures the coil keeps its magnetic field without constant power. Methods like eddy current and ultrasonic testing are used to check coil quality. These tests are common in industries like aerospace and energy.
Role of Automation in Ensuring Quality
Automation has changed how quality control is done in coil production. Smart systems use data from machines to find problems quickly. This reduces defects and makes production more consistent. Automated visual checks also improve accuracy and lower mistakes.
Advanced systems like SIPU's Fully Automatic Valve Coil Production Line use sensors to track production. These features make production faster and ensure every coil meets strict quality rules. Automation helps save money, reduce labor, and stay competitive in the market.
Tip: Use automated testing tools to make relays more reliable and lower defects during production.
Applications of Coils in Relays
Coils are crucial for how relays work. They help control electrical circuits easily and efficiently. Relays with coils are used in many areas, like factories and communication systems. Knowing the types of relays and their uses shows why they are so important in today's technology.
Types of Relays Using Coils
Electromagnetic Relays
Electromagnetic relays are very common. They use a coil to make a magnetic field. This field moves a part that opens or closes electrical contacts. This simple design makes them great for handling high-power tasks. You can find these relays in factories, where they control motors and power systems.
Why electromagnetic relays are useful:
They handle high voltage and current well.
Their design makes them reliable for many uses.
They work in many different applications.
Solid-State Relays
Solid-state relays don't have moving parts. They use semiconductors to switch circuits. These relays are quiet and last a long time. Unlike mechanical relays, they don't wear out quickly. This makes them perfect for places needing dependable performance.
Benefits of solid-state relays:
They last longer because they have no moving parts.
They switch faster than electromagnetic relays.
They need less maintenance, saving time and money.
Industries That Use Relay Coils
Automotive Industry
Cars use relays to control things like lights, windows, and air systems. Coils in relays make sure these systems work well. With more electric and self-driving cars, better relay production is needed.
Uses in cars include:
Controlling ignition and power systems.
Running safety features like airbags and brakes.
Helping electric cars save energy and last longer.
Fun Fact: Magnetic latching relays are now common in electric cars. They save energy and improve battery life.
Telecommunications
Relays are key in communication systems for fast and smooth switching. They help send signals quickly and keep networks running well. Coils in relays allow these systems to handle lots of data without problems.
Main uses in telecommunications:
Routing signals in phone systems and data centers.
Managing power for communication devices.
Supporting fast internet and mobile networks.
Industrial Automation
Factories depend on relays to run machines and processes. Coils in relays give the accuracy and dependability needed for automated systems. Whether it's a latching relay or a mechanical one, they keep things running smoothly in tough conditions.
Uses in factory automation:
Running conveyor belts and robotic machines.
Managing power for factory equipment.
Keeping circuits safe in dangerous areas.
Tip: Using advanced systems like SIPU's Fully Automatic Valve Coil Production Line can help meet the rising need for top-quality relays in these industries.
Benefits of Optimized Coil Production Lines
Improved Efficiency and Productivity
Optimized coil production lines make work faster and more efficient. Machines handle tasks like winding, insulating, and testing automatically. This reduces the need for people to do these jobs by hand. For example, modern machines can wind several coils at once, finishing faster than manual methods. Automation helps meet high production needs while keeping quality steady.
New technology, like programmable controls, keeps wire tension and layers accurate. This reduces mistakes and ensures every coil meets the required standards. Automation has cut labor costs by 75% and lowered material waste from 3% to 0.5%. These changes save time and make relays, including latching relays, more reliable.
Tip: Using systems like SIPU's Fully Automatic Valve Coil Production Line boosts efficiency while keeping quality high.
Cost-Effectiveness in Manufacturing
Optimized coil production lines help lower manufacturing costs. Automation reduces labor needs and cuts down on wasted materials. Machines use wire precisely, saving materials and avoiding mistakes. This is especially helpful for making latching relays, where accuracy is very important.
These systems also use less energy, lowering operational costs. Studies show energy use can drop by 85% with modern production lines. Fewer defects mean less money spent fixing or replacing parts, saving even more.
Note: Using optimized production methods saves money while keeping relays reliable and high-quality.
Scalability for Large-Scale Production
As relay demand grows, factories need to make more without losing quality. Optimized coil production lines can handle large-scale production easily. They can make different types of coils, including those for latching relays.
Modern systems, like SIPU's Fully Automatic Valve Coil Production Line, adjust to higher production needs. Features like multi-spindle winders and automated testing make scaling up easier. One factory increased production by 150% after using an optimized system. These systems help meet market demands and stay competitive.
Fun Fact: Factories with automated lines report 90% fewer defects and no safety issues, showing how reliable and safe these systems are.
By using scalable production lines, factories can make high-quality relays for industries like cars, telecommunications, and automation.
Enhanced Product Quality and Reliability
Making relays that work well is very important. Modern production lines use smart systems to improve quality and reliability. These systems help make relays, like latching relays, meet high standards.
One way to improve quality is by using surface inspection tools. These tools check for problems during production. For example, if a machine notices uneven wire tension, it alerts workers right away. Fixing issues early stops bad relays from being made. This keeps every relay meeting strict rules.
Another helpful method is predictive maintenance. Machines send data about their condition in real time. This helps find problems before they cause breakdowns. Maintenance can be planned ahead, reducing delays and keeping production smooth. Predictive maintenance also saves money by avoiding costly repairs.
Using data to make decisions is another smart way to improve quality. Production analytics track past and current data to find patterns. Dashboards compare batches to spot areas needing improvement. This ensures all relays, including latching relays, are made with steady quality.
By using these strategies, factories can make reliable relays every time. Whether making regular relays or latching relays, these methods help meet customer needs and stay competitive.
Tip: Use automated tools to catch problems early. This saves time and ensures every relay works perfectly.
Coil production lines are important for making relay parts. They help make components like latching relays quickly and accurately. Better production lines mean faster work, less waste, and steady quality. These upgrades make relays reliable for industries like cars and communication systems.
SIPU's Fully Automatic Valve Coil Production Line is a smart solution. It uses advanced machines and features to improve coil-making. This system helps factories meet high demands while keeping quality strong. It also helps businesses stay ahead in today’s busy market.
FAQ
What does a coil do in a relay?
A coil in a relay makes a magnetic field when powered. This field moves parts inside the relay to open or close circuits. In a latching relay, the coil helps it stay in position without needing constant power.
How is a latching relay different from a regular relay?
A latching relay stays in its position even after power is off. Unlike regular relays, it uses a magnet or latch to hold its place. This makes it great for saving energy in systems that don’t need constant power.
Why is automation useful in making coils?
Automation makes coil production faster and more accurate. It reduces mistakes, improves quality, and lowers costs. For latching relays, automation ensures the coils meet strict standards for performance.
Which industries use latching relays?
Latching relays are used in cars, communication systems, and factories. They control things like car ignitions, signal systems, and robots. These relays save energy and work well in tough conditions.
How does SIPU’s Automatic Coil Production Line help?
SIPU's system automates all steps of making coils, like winding and testing. It works faster, wastes less material, and makes high-quality coils for relays, including latching relays, in big factories.
What materials are needed to make relay coils?
Good copper wire and insulation materials like Nomex or Kapton are key. These materials help the coil carry electricity well and handle high voltages, which is important for latching relays.
Can better production lines save money?
Yes, better production lines cut costs by using less labor and materials. They also save energy and make it easier to produce more relays, including latching relays, to meet demand.